Actions that cause an unbalanced inventory
Here are the actions that usually causes an unbalanced inventory:
Action 1: Manual ajustments of the inventory when you can’t find the items.
Action 2: Not invoicing the same parts as the reception parts
Action 3: Purchasing parts excluded from the inventory follow-up: paper, soap, etc...
Action 4: Choosing the wrong options when reporting inventory value.
Action 1: Manual ajustments of the inventory when you can’t find the items
When manually changing quantities in your inventory, ajustment transactions ares generated to keep a track of your actions. You may consult the history of transactions of a product by clicking the button labeled “List of transactions” on his file.
Action 2: Not invoicing the same parts as the reception parts
For example, invoicing the part/product #5141 (-1 quantity) and receiving part/product #PH5141 (+1 quanity)
To garanty a better inventory follow-up, make sure to generate your purchases through the estimates, which will assure that the same products will be used for invoicing and receiving.
Action 3: Purchasing parts excluded from the inventory follow-up: paper, soap, etc...
When pulling out inventory reports, do not select categories with no inventory follow-up needed. Since GEM-CAR version 7.1, you can set categories to not include inventory follow-up by unchecking that option in your categories options. When they are all set, next time you pull out your inventory reports, the products in these categories will be excluded.
Action 4: Choosing the wrong options when reporting inventory value
When pulling out inventory reports, make sure to select the right options. here is an example of reports with different inventory balance based on the options selected:
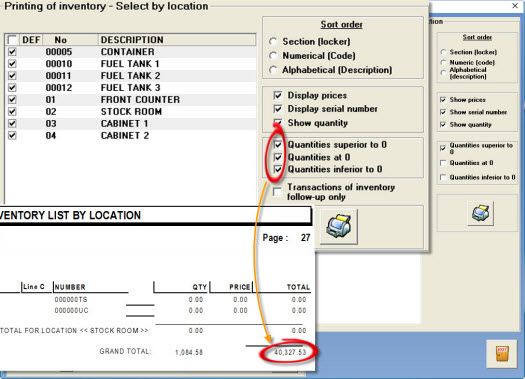
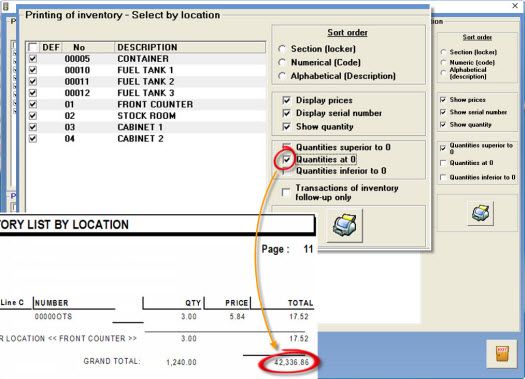
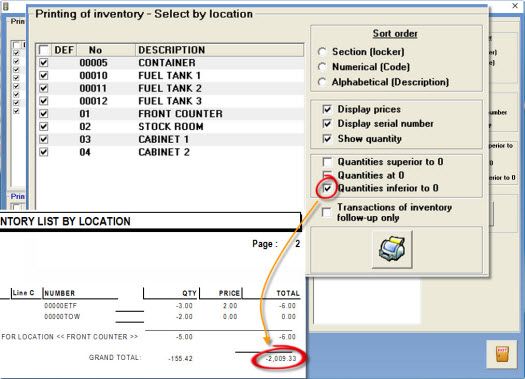